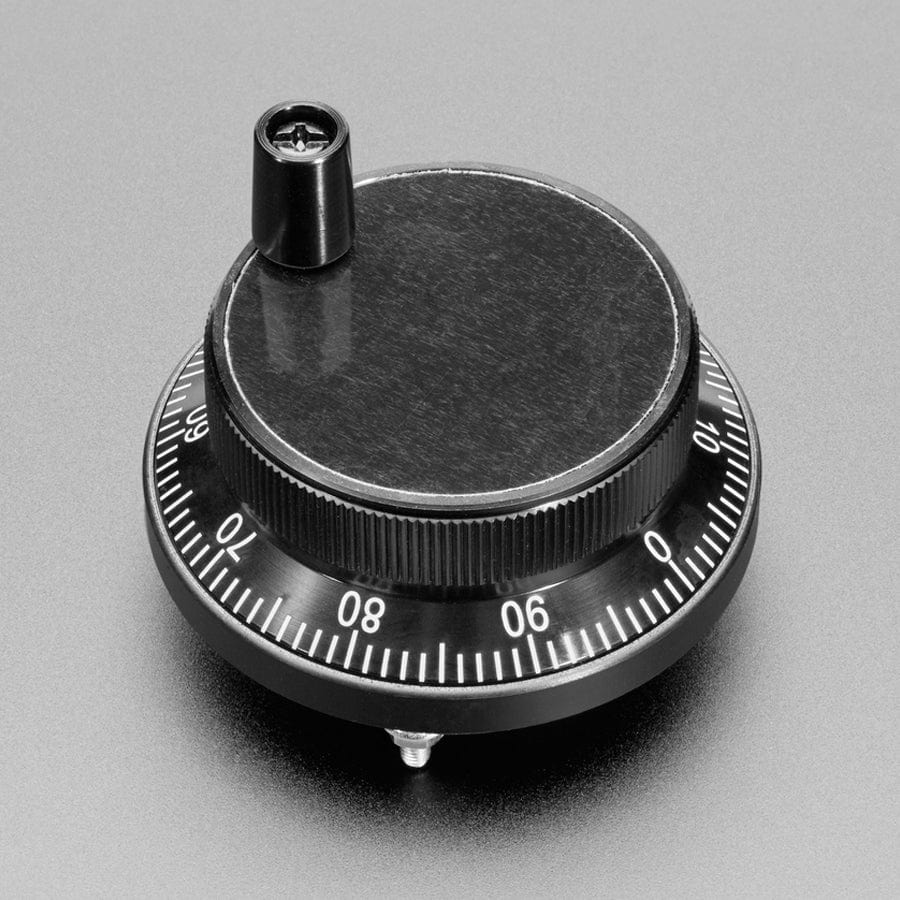
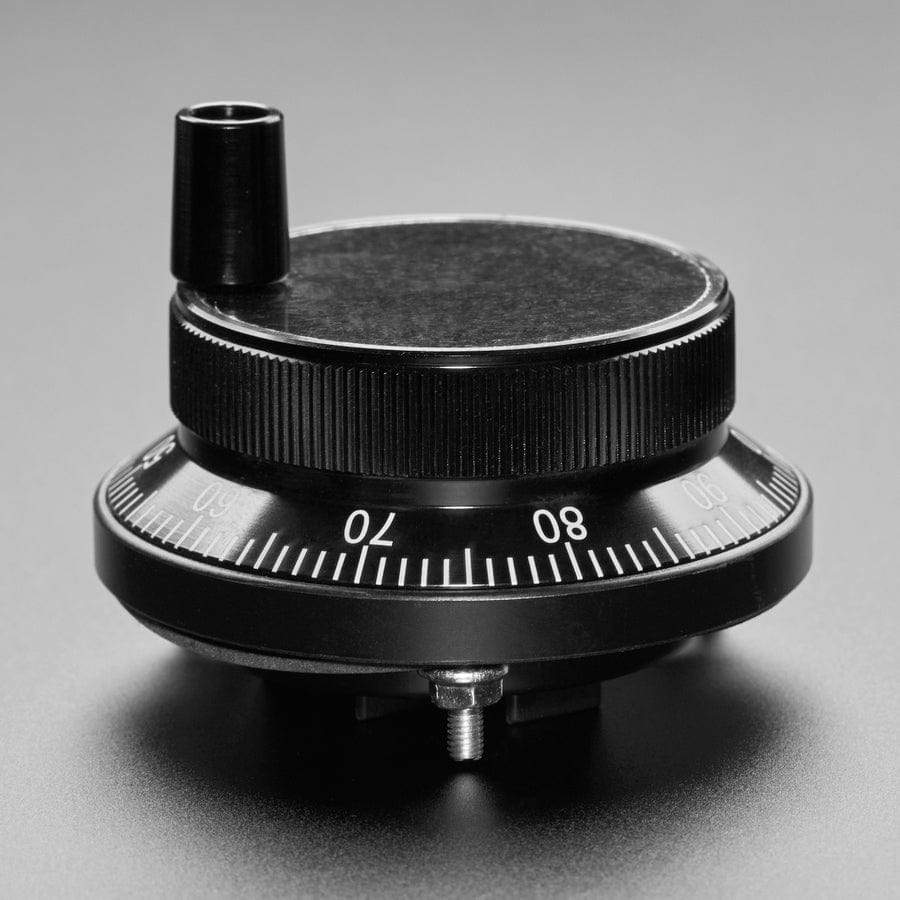
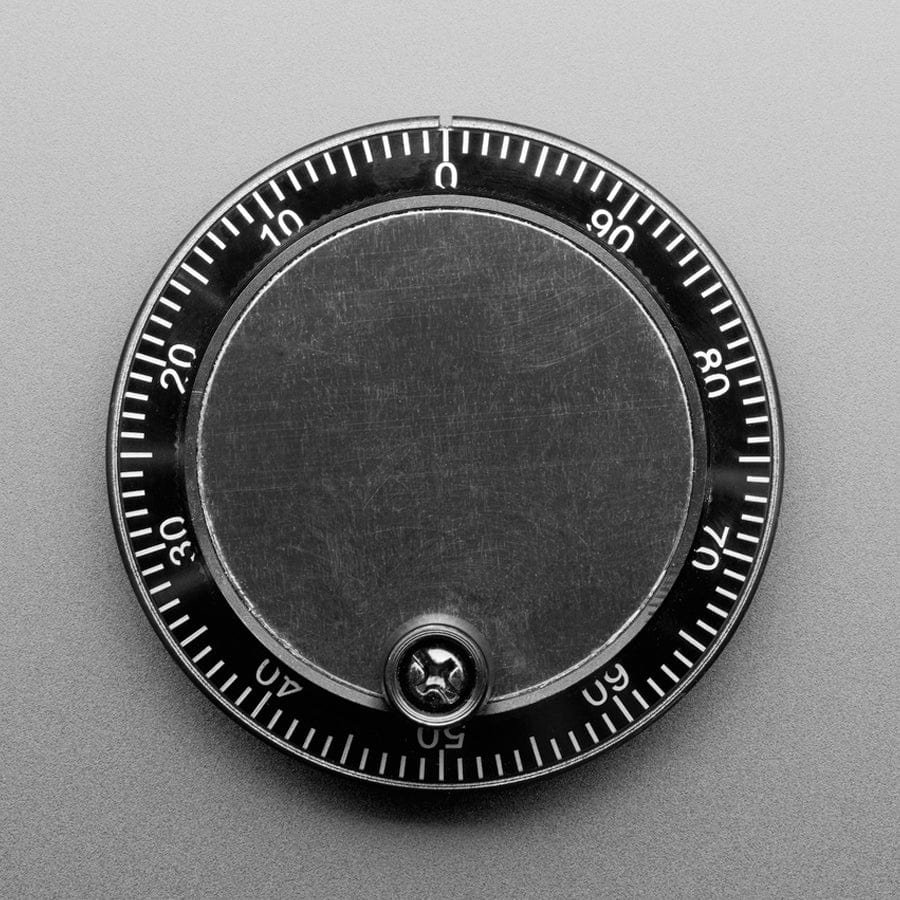
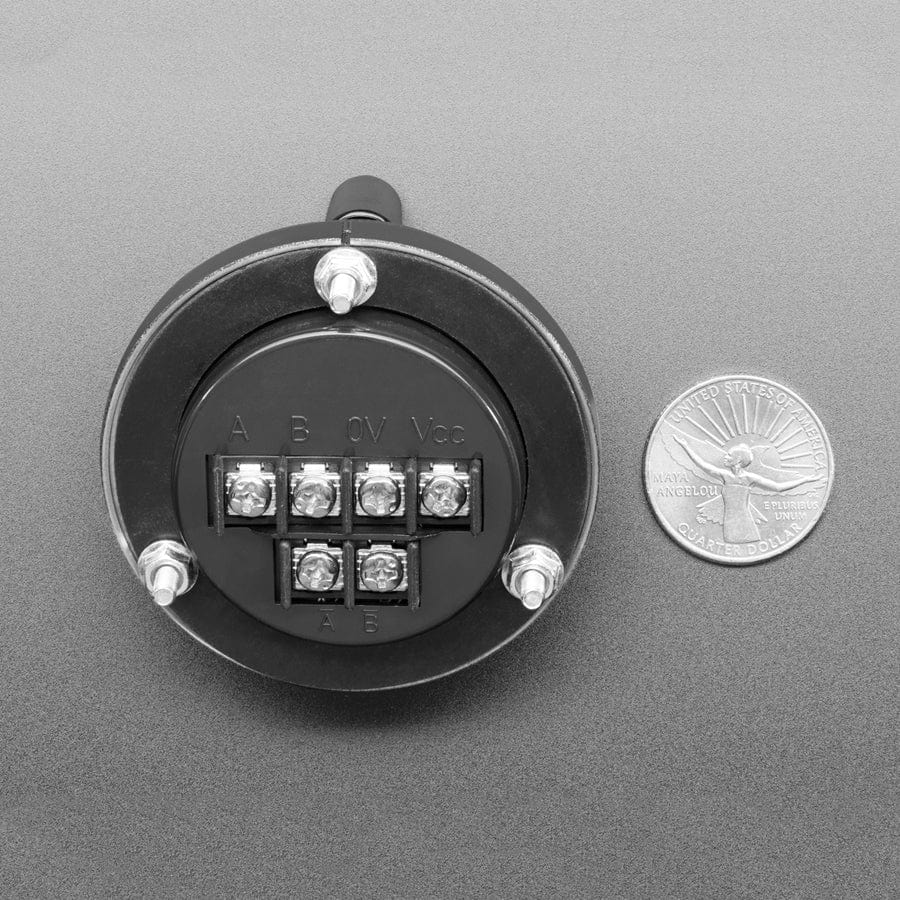
Login / Signup
Cart
Your cart is empty
We have various PCB-mount rotary encoders in the shop, great for making interfaces where you may want to spin a knob around to select a value. These large knobs are also encoders, but very large - like hand-sized! They're used for controlling CNC machines 'manually' - there are 100 ticks per rotation so each rotation can easily align with a centimeter or inch. But they're also really nice for any time where you want a large, 360-degree rotation, tactile interface.
Unlike PCB-mount rotary encoders, these encoders are not soldered directly to a board. Instead, there are screw terminal blocks on the back to connect wires. Provide any DC voltage to VCC (for the pullup/positive voltage), and ground, and read A and B for the relative direction & motion pulses. Once wired up, it works with any rotary encoder tutorial.
Rotary encoders are useful as rotation sensors or selectors and look similar to potentiometers. However they are not like potentiometers at all, so it's important to realise the difference! These rotary encoders rotate all the way around continuously and are divided up into 100 'segments'. Each segment has a clicky feeling to it, and each movement clockwise or counter-clockwise causes the two switches to open and close. There is no way to know what the current 'position' is - instead, you would use a microcontroller to count how many 'clicks' left or right it has been turned. If you need to detect rotational 'position' a potentiometer would be a better choice.